Smooth and disturbance-free operation of the coke oven machines is a key factor for efficient and economical coke making operations. USIT offers the state-of-the-art radar based Oven Identification and interlocking system(OIS) that ensures fast, reliable, accurate positioning and interlocking of coke oven machines. OIS releases the operator form complicated and time consuming scheduling work by continuously calculating the "next oven" to push and/or charge and sending the relevant information for the next pushing and charging time, together with the respective oven number to the coke oven machines for the operators to follow. OIS make the coke oven operations safe, smooth and close to the target.
- Scheduling
- Positioning
- Anti-collision
- Interlocking
- Challenges
- Features
- Benefits
Scheduling:
To supervise and manage the coke oven machine operation, a sophisticated oven pushing and oven charging schedule is provided. The production schedule of coke oven is affected by information such as production task, technological process characteristic of coke oven, equipment state and resource situation. It's an optimal control question with multi-object and many-restrains. When the unusual situation comes, coke oven production gets influenced and the production schedule of the coke oven is adjusted dynamically. OIIS ensures a disciplined charging and pushing operation by rule based schedule generation and is flexible enough to allow deviation from the schedule if a particular oven needs special treatment, maintenance etc. It guarantees pushing of coke and coal injection on the schedule, steady production operation and carbonization time, which improves coke quality and lengthen the furnace service life.
Positioning:
Since the travelling machines carry heavy loads at high speed, precision position control in one go is very difficult. Therefore the positioning of the machine is performed in two steps, gross control and precision control. When the machine is travelling on the rail, it recognizes each oven number and finds its gross position. After the machine reaches its required gross position, precision position control is activated that calculates the deviation between the center position of target oven and the machine and reduces the position error within a tolerance.
Anti-collision:
Machine collisions can not only be severely dangerous for operators on the machines but in most of the cases cause a long production stop to determine and repair damages. In most of the cases, it is difficult or impossible to compensate such a breakdown of a machine. This breakdown results into production losses. Radar is therefore an inexpensive insurance against such losses. With one set of hardware, both position and collision avoidance is provided simultaneously. This combines the reliability of radio sensors with the increased safety at a fraction of the cost for independent systems.
Anti-collision functionality is provided by display of real time distances on HMI to enable the machine operator to take appropriate action or to provide warning or stop signals to the machines.
Interlocking:
All the coke oven machines continuously communicate their position to the OIIS software running on the server at the control room. The remote OIIS software running on the HMI of the oven machine identifies the oven no. where coke oven machine has reached based on the readings provided by it's radar. Remote OIIS software also identifies the direction of movement and the distance to be traveled to reach the target oven. The position of other machines in the remote OIIS software of the coke oven machine is continuously updated by OIIS software running at the server.
Signal for pushing operation is released to the pusher car only when the guide car and the quenching car are aligned at the oven to be pushed. Similarly, the cross battery interlocking coordinates between the pusher car and charging car for operating the leveler drive during charging. This eliminates all possibilities of wrong pushing, thereby improving safety of employees and equipments.
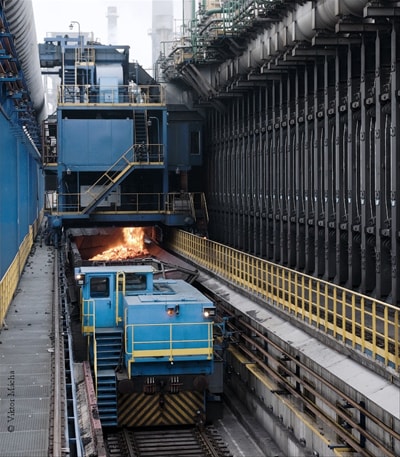
Historically, process automation systems have been challenged by environmental factors limiting the application of the most diverse solutions available. At the coke oven plant, these factors are sometimes even more challenging due to the nature of the coke manufacturing process, its environments and the status of many facilities/machines which have been operating for a long period of time.
Operation of coke oven machines typically known as charging cars, pushers cars, guide cars and quenching cars requires a perfect coordination between the top side, pushing side and coke side in order to effectively follow the manufacturing schedule avoid accidents. To achieve this level of coordination, operators play a vital role, since they perform not only the movement to place the machines where required, but also the final positing for alignment with the oven and the communications (typically via radio) with other machine's operators to make sure everything is in place for starting a charge or a push. Several preceding attempts have been performed at the battery using optical, mechanical, RFID and laser sensors, to effectively detect the oven at which machines were located, as well as to help the operator to precisely position the machine at the right spot in front ot it. After being in operation for some time, all these technologies has been discounted due to the high maintenance and calibration efforts, malfunctioning in the presence of dust, vibrations, heat, steam, snow, rain, etc. periodic failures and high installation etc.
Your Expectations :
- Avoid wrong pushing be identifying the correct oven and positioning the machines with an accuracy of ±1mm.
- Precision prefect signal for pushing or charging operation by aligning and interlocking all machines with the oven scheduled for operation.
- Perfect coordination between the top side, pushing side and coke side in order to effectively follow the manufacturing schedule and avoid accidents.
- Real-time communications with other machine's operators to make sure everything is in place for starting a charge or a push.
- Dynamic production scheduling by monitoring real time operation.
- Robust system design for using at coke oven batteries under high temperature surroundings
- Precise and exact determination of position under harsh conditions unaffected by dust, vapour, heat, mist, etc.
- Time-saving through exact positioning increase the number of oven cycles
- Cross battery interlocking and authorization
- Direct interlocking and machinery control with low reaction time
- Increased safely by auto-positioning of equipment and cross battery interlocks
- Integration with real time system for online monitoring and control
- Increased safely
- Increased productivity
- Increased scheduling efficiency
- Better utilization of equipment
- Better consumption and dispatch plan
- Real time measurement and data processing
- A complete visibility