Wagon Loading System provides a high-precision train loading system, using wagon and material-specific optimized loading profiles as per the rated capacity declared by the government and available residual material inside each wagon. To measure the exact volume/weight of the wagon and online filling height of the wagon, USIT uses 2D radar technology. The system also gets connected with the existing railway system to exchange information.
- Challenges
- Features
- Benefits
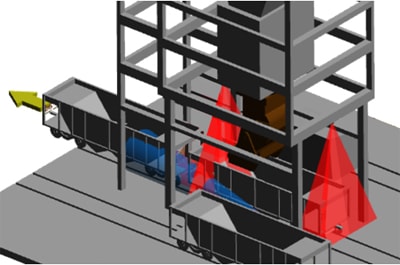
Identification of Residual Material :
Train loading stations can be the bottleneck for bulk material. Wagon capacity utilization, existing residual material inside a wagon, time to fill a wagon, identification & sequence of wagon and spillage while shifting wagon are few challenges which directly impact on the overall performance and profitability. The wagon loading becomes costly when the above parameters are not known on time. The radar based USIT system takes care of all the parameters. The auto scanning of wagon, auto identification of edge frame of wagon, scanning of residual material if any, prediction of volume as per rated capacity minus residual material lying inside wagon are some of the key functions to optimize the loading facility.
Spillage
Spillage of material during loading of wagon is a major concern. It happens when the height of the material is not inline with the rated capacity and when the chute gets shifted to new wagon. In absence of the real time filling height measurement system, the operator works on eye estimation which results into either under loading or overloading of the material. In case of under loading, less material is getting loaded & transported whereas overloading of material means spillage while moving the train as well as demurrage. The chute gate should be shifted only when the mouth of the chute is on top of wagon where material has to be filled. In absence of real time position and edge frame of wagon measurement system, the slide gate of the chute gets shifted earlier than expected which results into spillage. The loading station reports 3 to 4% of spillage of material every rake/wagon.
- High-precision 2D Radar scanners to efficiently scan empty & loaded wagon
- Identify incoming wagons by type (differing dimensions) and their sequence no.
- Detect the edge frame of incoming wagons (irrespective of type).
- Measure the volume of residual materials from previous loads in the incoming wagons.
- Measure the volume of material passing through the belt at the rake loading station.
- Detect the height and volume of the filled material to allow for filling to maximum load height and shift the filling chute to next wagon.
- Measure the moving speed of the rake loading machine in real-time.
- Measure the gap between filling wagons and reduce the spillage of material during shifting loading from one wagon to another.
- Stabilize the loading capacity of each wagon at loading point.
- Detect the speed, misalignment and the gap between cord rim and coke of the conveyer belt.
- Identify the evenness of the material after being loaded.
- Full volumetric inventory control of the inventory loaded in the wagon at all times.
- Detect and depict the 3D profile of the material in the wagon.
- Interface with other system to exchange data/information.
- Optimal utilisation of wagon capacity reduced transport cost
- Shorter lead time - increased manpower utilisation
- Full wagon utilisation without risk of overloading - control demurrage cost
- Reduced/eliminate demurrage - increased profit margin
- Reduced spillage - reduced wastage
- Reduced operator staff - Manpower saving